The control system consists of elements like Programmable Logic Controller, Input/Output cards, barriers, flow computers, relays, motor soft starters and UPS. These can be housed in a special conditioned container, with dimensions varying according to customer specifications.
Operators miss nothing with precise control across the full range of operating pressures and temperatures. When they need it, there’s remote assistance and diagnostics across the web.
The control panel can be operated locally, or remotely from another site. Petrogas can supply data communications to the main plant control room.
EASIER
Remote support for distributed control systems is possible during maintenance operations.
Alarm reporting uses smart messaging to signal maintenance requirements with critical reporting (for predictive maintenance settings on component level), enabling predictive maintenance based on Key Performance Indicators of the system.
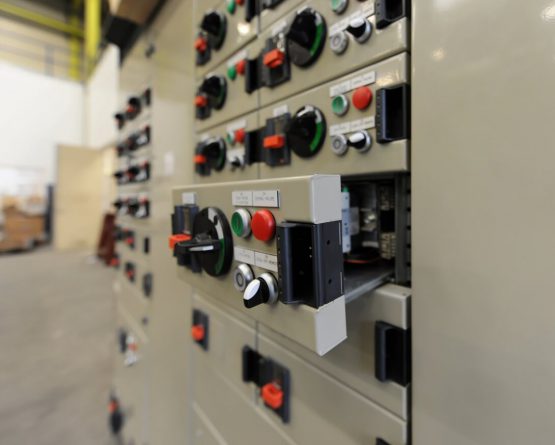
SMARTER
Software is designed using customizable modules per component. It is ISA 95 ready to reduce the costs, risks and errors associated with implementing interfaces between enterprise and production control systems.
ISA 95 compliance ensures that you have easy access to the critical information to get a better insight to KPIs like Mean Time Between Failures. It also ensures that you can easily exchange this information with other systems. You can fine-tune maintenance programs to reduce risk, errors, downtime and costs.
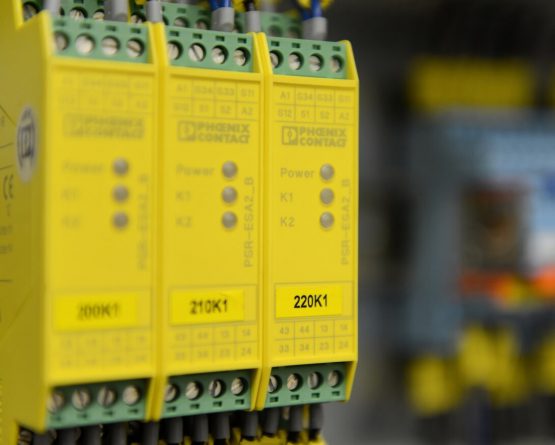
BETTER
The control philosophy conforms to ANSI/ISA-88 (S88). This defines hierarchical recipe management and process segmentation frameworks to separate products from the processes that make them.
The standard enables reuse and flexibility of equipment, and provides a structure for coordinating and integrating recipe-related information across the traditional ERP, MES, and control domains.
A key aspect of S88 is to enables the modularization (segmentation) of processes. It’s this modularization that enables both flexibility and reuse of recipe components and equipment control components
The increased flexibility lets the manufacturing process accommodates more products with faster changeover to different components. It means faster time-to-market, and ROI increases with each subsequent project for both end users and suppliers. The modularity and replication reduces need to design and create everything from scratch for every new process developed).
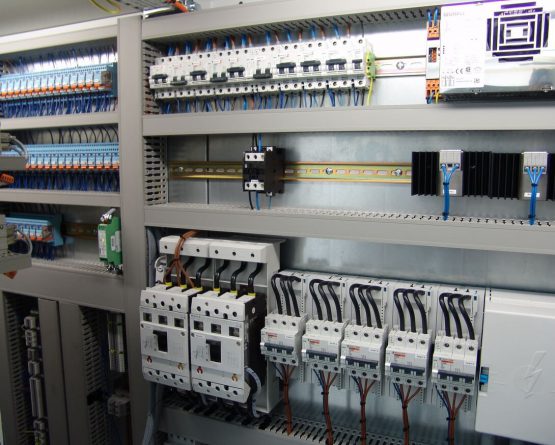
Case studies
Strong local network
Al Diwaniya fuel gas conditioning station
- What did our customer request?
-
Our customer required a fuel gas conditioning station for the Al Diwaniya project. The station prepares and conditions the gas before it enters the turbine, ultimately to generate electricity. The conditioning entails filtering, heating and reducing the pressure.
- Our solution
-
Petrogas supplied the Fuel Gas Conditioning Station, including hardware and control systems. A fuel gas metering system measures the gas used, and a safety valve shuts down the gas supply in case of extreme pressures or temperatures.
- What set the project apart?
-
Petrogas also performed part of the overall engineering. From our experience in similar projects, we advised the customer to approach a number of things differently to improve safety and efficiency.
- What were the project challenges?
-
“Al Diwaniya is located around 250 km south of Baghdad, in a region with security risks. Thanks to our local network of qualified professionals we assembled and commissioned the system on site. An innovative design meant we could easily mount the skids against each other on site, leaving just the bolts and nuts to be tightened.”
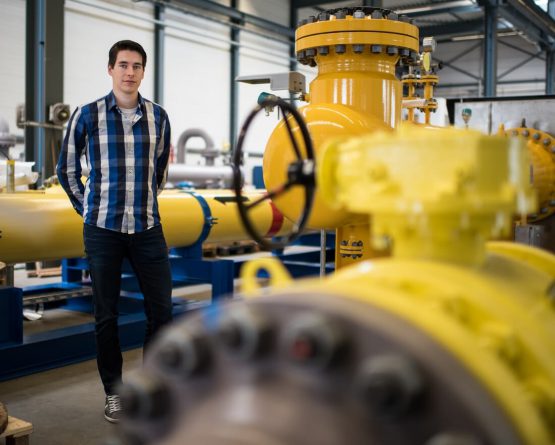
Contact us
Would you like to discuss your project with our Experts? Please feel free to contact us.
Direct contact with our Experts
Your interest
Control System
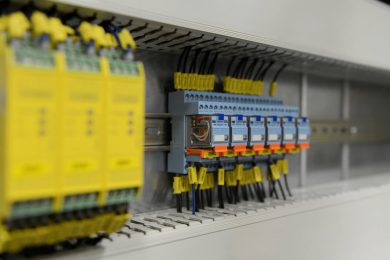