The gas inlet valve section, also known as the Emergency Shut Down (ESD) or Safety Shut Off Valve (SSOV) section, is a crucial safeguard system in any gas conditioning system. The inlet valve section can seal off the gas system from the gas supply pipe, to safeguard the entire downstream plant in case of an emergency. The ESD valve shuts off the gas supply automatically on a downstream alert, and can be opened or closed from a central control room or locally at the ESD valve. The fuel gas inlet design easily adapts to single line (1×100% gas flow), dual line (2×100% gas flow), or other configurations.
The upstream and downstream pressures of the inlet valve are equalized to prevent the ESD valve seals from excessive wear.
We use state of the art components to guarantee plant safety at all times. The main inlet valve allows pigs to pass through, and has various options in different makes and types of fail-safe actuators, including:
- Electric Actuators, with fail-safe controls
- Pneumatic Actuators, operated by instrument air or instrument gas which is conditioned at a take-off point downstream of the valve.
- Gas-over-oil actuators, to allow reliable operation on sour and wet fuel gas.
EASIER
Our inlet systems for gas treatment plants range from compact, self-controlled valves up to fully automatic systems that need only supervisory monitoring and operation from a control room.
The equipment is reliable by design to reduce the need for servicing. We can also help with preventive and predictive maintenance. The main valve can be isolated for maintenance, with the ‘system in a box’ skid design making for easy access.
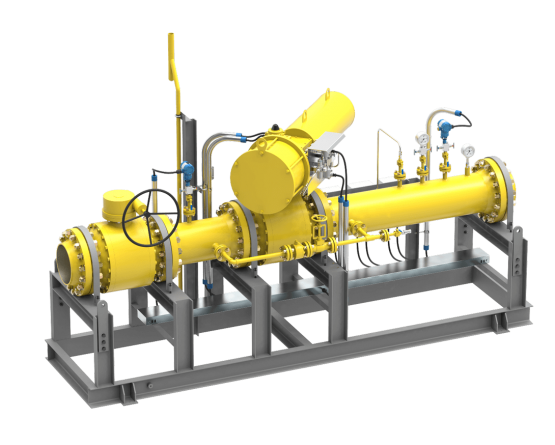
SMARTER
Our innovative inlet designs for gas treatment plants maximize efficiency for lowest total cost of operation. For example, there’s no need for an external air source when our units are instrument-gas actuated.
We will optimize the pipe layout for minimum pressure loss too. We use the smallest possible pipe dimensions to create some of the industry’s most compact (and lowest cost) systems which can still easily maintain the required gas flow.
Other smart aspects are a main valve that can be isolated for maintenance, and that control features can offer single, double or triple redundancy.
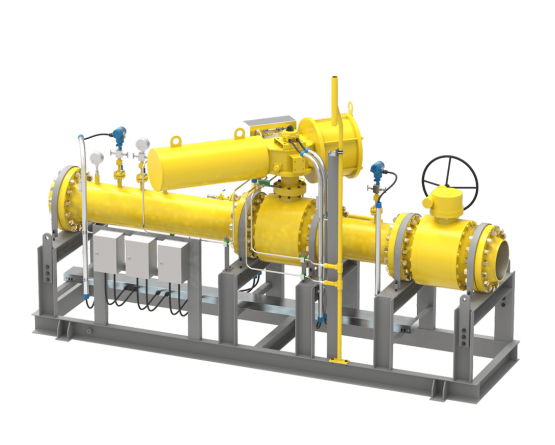
BETTER
The huge throughput’s of gas conditioning systems mean that small changes in layout or gas conditions like temperature and pressure can create significant changes in pressure losses. Your inlet system is therefore designed to suit the individual gas source and turbine. The ESD valve section will safeguard downstream equipment from sudden excessive changes in the gas flow that have the potential to damage downstream equipment.
Petrogas excels at designing the best layout for minimum pressure loss and so maximum gas flow for the available plot size. We adapt and optimize our designs to precise customer requirements, even down to the make and type of components.
Turbine operators can’t afford downtime, and our inlet systems can include double or triple redundancy for highest availability. Operation is automatic, with manual override using proven and reliable technology based on quality components from world-class suppliers.
Our inlet systems can be SIL (Safety Integrity Level) certified to your particular preferences. They can also be designed for harsh environments, and resist temperature extremes of -46°C to 100+°C and high concentrations of hydrogen sulphide and other pollutants.
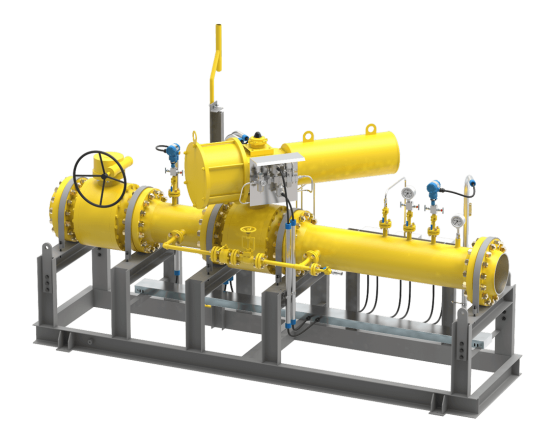
Case study
Short 32-week turnaround time
Fuel gas inlet station for power plants
- What did our customer request?
-
This project was part of an agreement between Siemens and the Egyptian government to add 50% more energy to the power grid within a number of years. We were asked to supply the Fuel Gas Conditioning Station for three of the prospective power plants (Beni Suef, Burullus and New Capital). After completion in May 2018, the three power stations will be the largest gas-fired, combined cycle power plants ever built and operated in the world. And they will supply enough electricity for 45 million people.
- Our solution
-
Petrogas delivered the fuel gas systems for the 24 H-Class gas turbines, designing, engineering and fabricating the system sections. In particular, we developed a custom DRIP-barrel (horizontal liquid separator) and also supplied Emergency Shut-Down, inlet filters, electrical heaters and control cabinets.
- What set the project apart?
-
We usually build all the pressure vessels and pipes in our own workshop in Eindhoven, the Netherlands. Because of the size of the project, though, we outsourced part of the production to some of our expert subcontractors.
Together, we helped Siemens to set a new worldwide benchmark for the execution of a fast-track power generation project. After completion of the first phase Siemens was already able to connect 10% more power to the grid than forecast, a surplus sufficient to supply electricity to an additional one million people in Egypt.
- What were the project challenges?
-
“The short turnaround time was a real challenge. For a project like this it is usually 10 to 12 months, but we delivered the installation within 8 months. Siemens was delighted with the result and the plants actually achieved first-fire well ahead of schedule.”
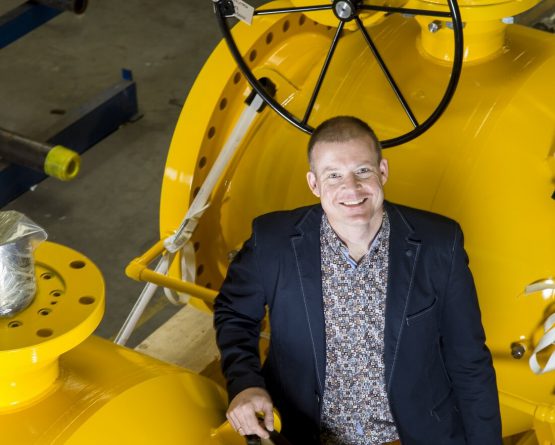
- What did our customer request?
-
Cegelec needed more electric capacity at a petrochemical industrial complex on Das Island off the coast of Abu Dhabi. Petrogas was asked to supply the fuel gas conditioning units for the natural gas powered turbine generators. These units ensure that the gas arrives at the gas turbines under the right conditions.
- Our solution
-
The natural gas was being sourced from different locations, so there were differences in pressure, composition and temperature. Gas from one of the suppliers also had high acidity. Petrogas supplied the installation to filter and heat the gas and reduce the pressure.
- What set the project apart?
-
The limited amount of space on the island meant the installation had to be as compact as possible, while leaving enough room for operation and maintenance.
- What were the project challenges?
-
“Initially, the requirements for the fuel gas conditioning units were fairly basic. But as the project progressed, several new key design requirements became evident. We pride ourselves on our versatility, and responded quickly to incorporate all the additional demands.”
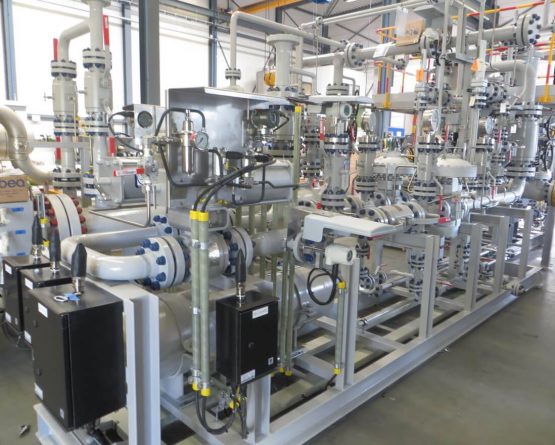
Dedication and hard work
Ras Al-Khair Power Plant (fuel gas system)
- What did our customer request?
-
The Saline Water Conversion Corporation is a Saudi Government Corporation responsible for producing electric power and desalinating seawater. The SWCC Ras Al Khair project was at the time the largest combined power and desalination plant in the world and won the prestigious “Desalination plant of the year” award in 2015. It is a landmark project for SWCC.
The plant converts more than 1 billion litres of seawater into potable water each day, transforming the potable water situation in Riyadh, one of the world’s fastest growing and most water-stressed cities. The plant also produces 2400 MWe of electricity for the Eastern Province of Saudi Arabia and helps to power the nearby Ma’aden/Alcoa Aluminium plant.
The power plant is gas & oil fired, and Petrogas won the contract for the fuel gas conditioning station with 1 million Nm3/h capacity for 12 gas turbines, along with the backup fuel oil system to ensure a high quality, reliable and continuous supply of fuel for the turbines. Waste heat and reverse osmosis are used to desalinate 1 billion litres of sea water per day. - Our solution
-
In close cooperation with the owners’ engineer Pöyry, we designed six identical blocks. Each had two mirrored gas conditioning systems including Emergency Shut-Down valves, filters, flow meters, heaters, pressure reducing systems for GTs and boilers, pressure boosting compressors and a high pressure gas buffer system. Petrogas built the skid-based system in workshops in the Netherlands and China, and erected and commissioned the system on site.
- What set the project apart?
-
Because Petrogas has both engineering and fabrication in-house, our customer benefitted from our practical experience in the initial basic design phase. The design was optimized before Petrogas built the skids, wrote the control software and performed the on-site commissioning.
The system can boost gas pressure for a prolonged period and can maintain gas supply for several minutes when the gas feed is interrupted to allow the turbines to switch to fuel oil. Petrogas played a substantial role in drawing up the operating philosophy between all these systems. - What were the project challenges?
-
“The sheer size of the project made it a challenge. The system is actually twelve complete 12” gas conditioning systems with 100% redundancy. The photo shows the stacks of the Water Bath Heaters, 36 in total.
Resources, planning, logistics between several workshops and dozens of suppliers all required a creative approach. The order came in 2011 when we already had a healthy backlog, and the order was worth about a year’s turnover. Petrogas successfully completed the job thanks to the dedication and hard work of our personnel and suppliers. “
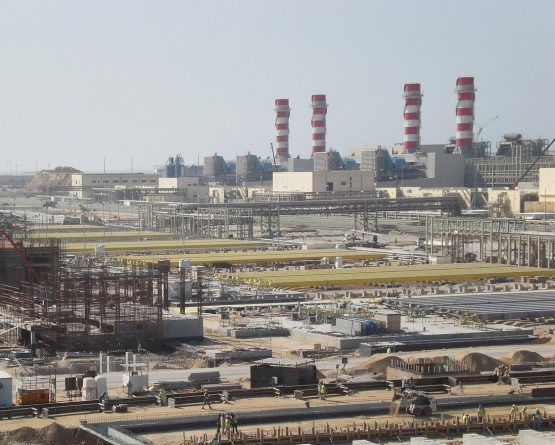
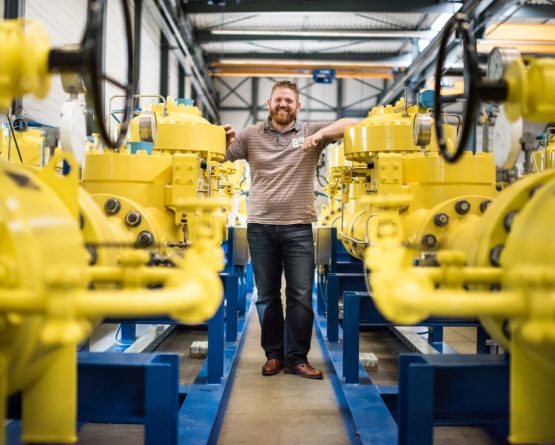
Contact us
Would you like to discuss the gas inlet options for your project with our Experts? Please feel free to contact us.
Direct contact with our Experts
Your interest
Gas Inlet
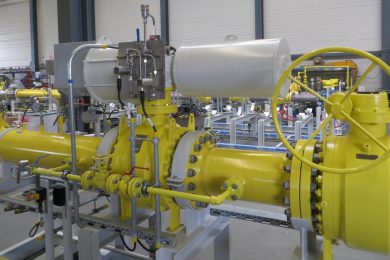