The buffer system consists of a high pressure compressor, a buffer volume and an outlet system (usually a heater and pressure reducing system). The goal is to store enough gas to keep the gas turbine running if the gas supply is interrupted. The buffer must provide gas for long enough to allow the turbine control system to perform actions like switching over to backup fuel (usually diesel), start pumps and adjust burner settings. The buffer volume is optimally sized for each project, since each combination of gas pressure, consumption and composition requires a different volume.
The compressor feeds gas into the buffer volume at a high pressure (80-100 barg). If the inlet pressure drops and the online pressure reducing system fails to supply enough pressure, the buffer reducing valves automatically supply the gas and signalling the main control system the fuel switchover is to be initiated.
- Ideal type and make of compressor are specified for each project (Petrogas works brand independant)
- Oil-free compressors prevent fuel contamination
- There are multiple cooling options
- The buffer volume is not only sized per project, available plot size is also factored in. Vertical gas vessels or stacked piping is an option to save space
EASIER
Operation is automatic, with self-operating filling, refreshing and depletion controls. Adding a buffer to the fuel gas supply system allows for easier switch-over to secondary fuels.
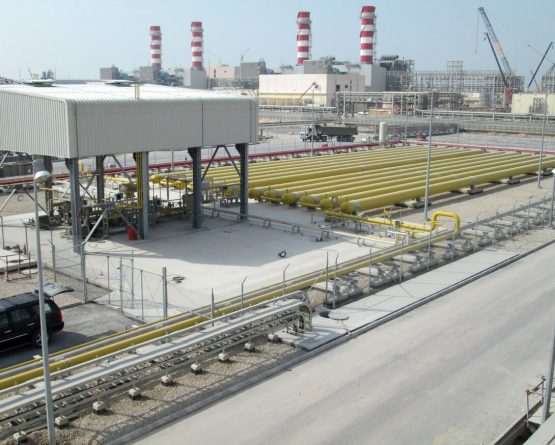
SMARTER
We can package bare compressors on skid or in a container. Compressors can be installed in full enclosure or under a shelter.
Smart buffer design allows materials to expand during temperature changes. The buffer is sloped to prevent liquid condensate build-up, and the buffer volume refreshes to prevent excessive Wobbe variations. Adding a buffer to the fuel gas systems reduces downtime for turbine operators and allows for continuous production during switch-over.
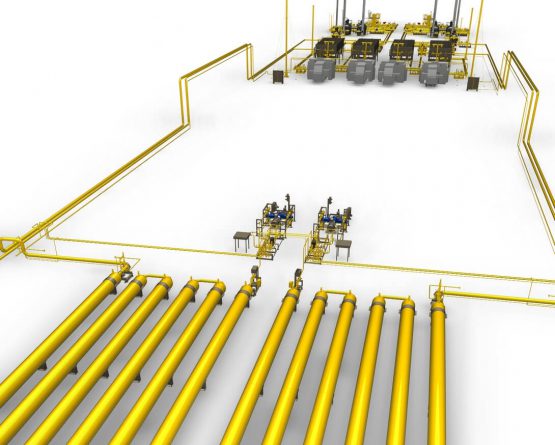
BETTER
We calculate the optimum project-specific buffer volumes, and the optimum volume vs steel-weight ratio, the optimized design reduces the CAPEX cost and ensures all requirements are met. Interlocks in the design prevent unintentional start-ups.
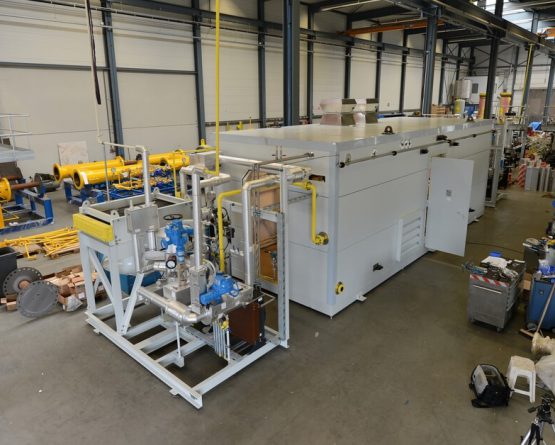
Case studies
Dedication and hard work
Ras Al-Khair Power Plant (fuel gas system)
- What did our customer request?
-
The Saline Water Conversion Corporation is a Saudi Government Corporation responsible for producing electric power and desalinating seawater. The SWCC Ras Al Khair project was at the time the largest combined power and desalination plant in the world and won the prestigious “Desalination plant of the year” award in 2015. It is a landmark project for SWCC.
The plant converts more than 1 billion litres of seawater into potable water each day, transforming the potable water situation in Riyadh, one of the world’s fastest growing and most water-stressed cities. The plant also produces 2400 MWe of electricity for the Eastern Province of Saudi Arabia and helps to power the nearby Ma’aden/Alcoa Aluminium plant.
The power plant is gas & oil fired, and Petrogas won the contract for the fuel gas conditioning station with 1 million Nm3/h capacity for 12 gas turbines, along with the backup fuel oil system to ensure a high quality, reliable and continuous supply of fuel for the turbines. Waste heat and reverse osmosis are used to desalinate 1 billion litres of sea water per day. - Our solution
-
In close cooperation with the owners’ engineer Pöyry, we designed six identical blocks. Each had two mirrored gas conditioning systems including Emergency Shut-Down valves, filters, flow meters, heaters, pressure reducing systems for GTs and boilers, pressure boosting compressors and a high pressure gas buffer system. Petrogas built the skid-based system in workshops in the Netherlands and China, and erected and commissioned the system on site.
- What set the project apart?
-
Because Petrogas has both engineering and fabrication in-house, our customer benefitted from our practical experience in the initial basic design phase. The design was optimized before Petrogas built the skids, wrote the control software and performed the on-site commissioning.
The system can boost gas pressure for a prolonged period and can maintain gas supply for several minutes when the gas feed is interrupted to allow the turbines to switch to fuel oil. Petrogas played a substantial role in drawing up the operating philosophy between all these systems. - What were the project challenges?
-
“The sheer size of the project made it a challenge. The system is actually twelve complete 12” gas conditioning systems with 100% redundancy. The photo shows the stacks of the Water Bath Heaters, 36 in total.
Resources, planning, logistics between several workshops and dozens of suppliers all required a creative approach. The order came in 2011 when we already had a healthy backlog, and the order was worth about a year’s turnover. Petrogas successfully completed the job thanks to the dedication and hard work of our personnel and suppliers. “
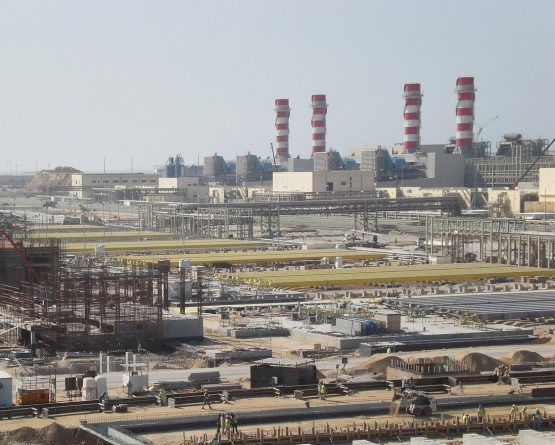
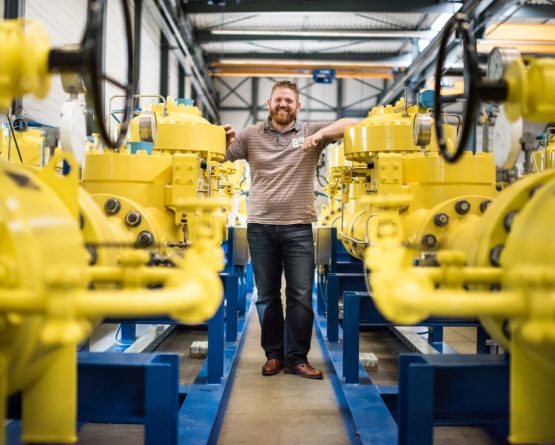
Contact us
Would you like to discuss your project with our Experts? Please feel free to contact us.
Direct contact with our Experts
Your interest
Buffering
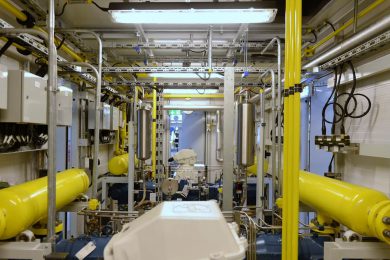