Our Approach
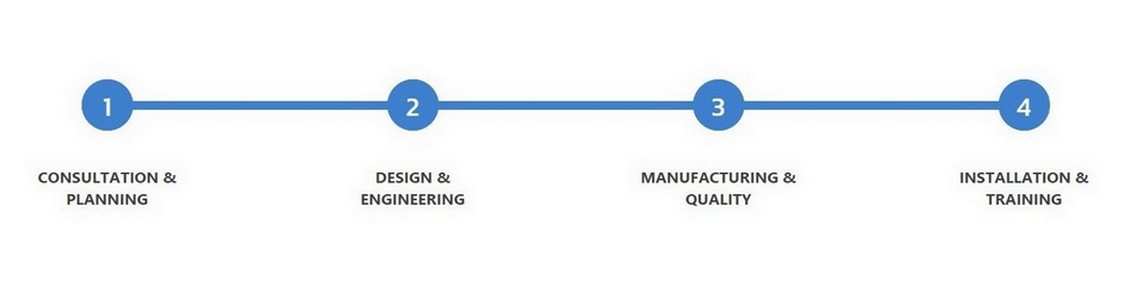
Case studies
Compact design, fit for airfreight
Sand Removal system for the 3-phase separator on Sakhalin
- What did our customer request?
-
On the Sakhalin site, a vessel that separates water, oil and gas also accumulated sand over time. The sand could only be removed by stopping the process and physically going inside the vessel.
ENL wanted a system that could remove this sand without the need to stop the process. Sulzer Chemtech developed this and requested the help of us for the mechanical engineering, the fabrication of the installation and the procurement of the required components.
- Our solution
-
We designed a water circulation skid which included as many of the required components as possible to minimize the work to be done at site.
- What set the project apart?
-
This is the first project where the Sand Removal system has been implemented on an existing site. It was a prestige project that also had a very short lead-time. There were four parties involved that needed to collaborate to make this project a success; us as Petrogas, our client Sulzer, their client Fluor and the end user ENL. The first two months there were conference calls with all these parties every day to closely monitor the progress and discuss any risen issues.
- What were the project challenges?
-
The very short lead time, which is a challenge to begin with, also caused the requirement to transport the installation by air freight. Normally that should not be a problem, but in this case it had to be transported to Sakhalin Island, on which limited size aircrafts can land, which greatly impacts the maximum dimensions per piece of cargo. Next to this, the available plot for the water circulation skid was quite small as well.
Other companies might have decided to just send the loose materials to site and build it on location. But Petrogas, excelling at skid solutions, designed two boxes that could be transported by air and easily be connected to each other on location, containing the majority of the piping and components that made up our scope of the system.
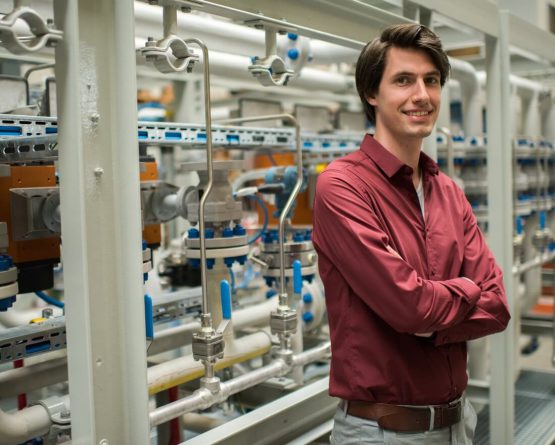
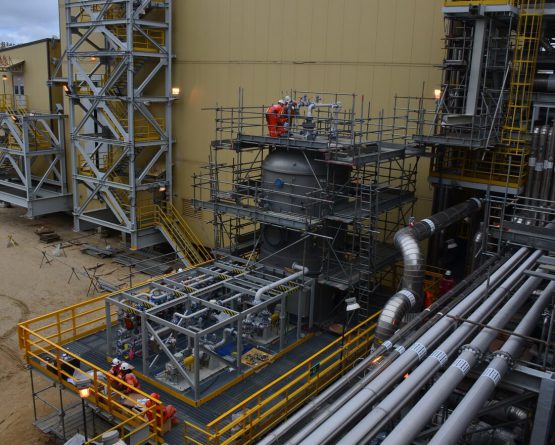
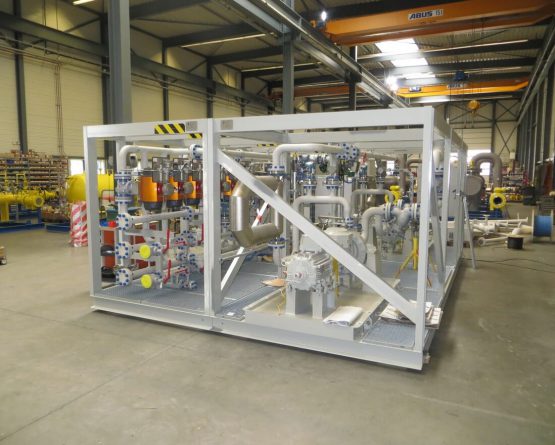
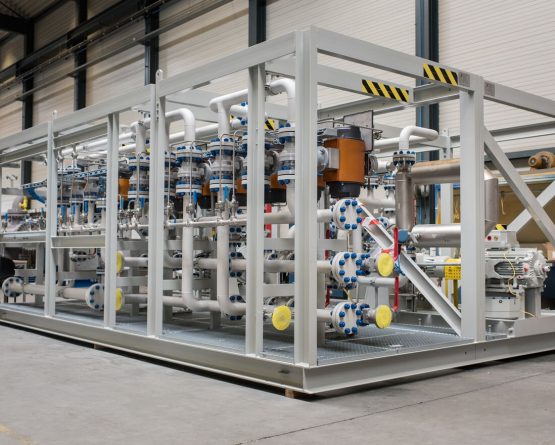
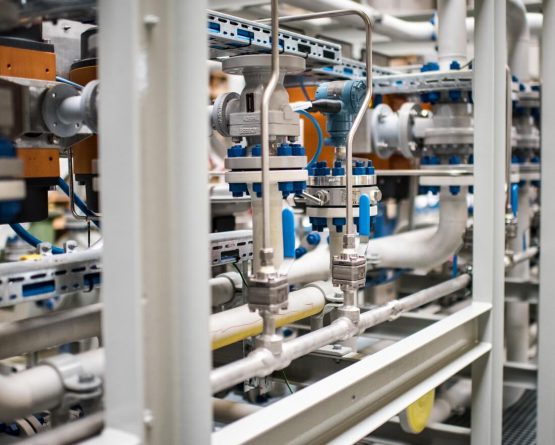
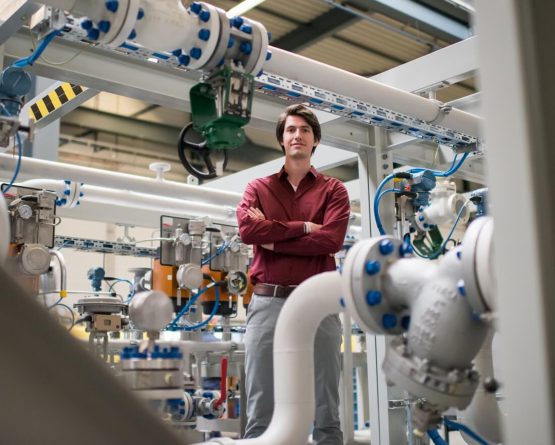
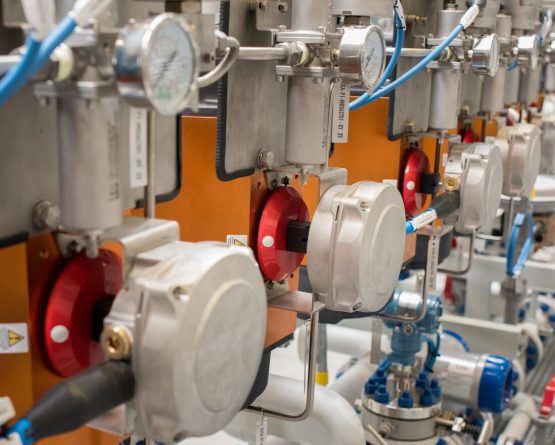
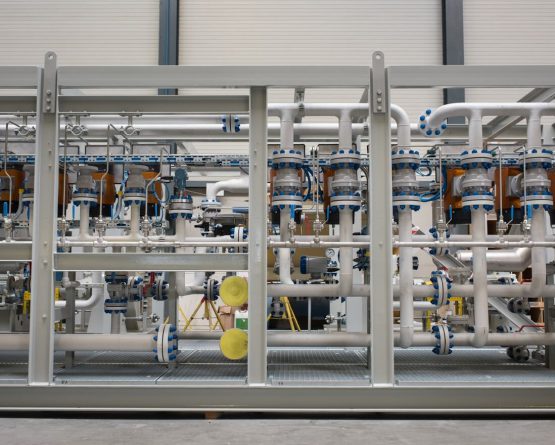
Complex project management
Thermphos phosphorus removal project
- What did our customer request?
-
After the Thermphos phosphorus plant went bankrupt in 2012, the administrators and the province of Zeeland (Southern Netherlands) issued tenders to dismantle the complex and remove all the phosphorus. The entire project was secured by Decontamination Services, a subsidiary of Mourik. Petrogas was asked to process 4000 tons of stored sludge, which contained phosphorus and was slightly radioactive.
- Our solution
-
We designed, built and operated the custom processing installation for the phosphorus-containing sludge. The composition of the material made it necessary to design a special pump (phosphorus auto-ignites around 30°C). By subjecting the sludge to a 40 bar pressure the liquid phosphorus and water were separated from the solid components, which were then pressed together to form a cake. The liquid phosphorus was reusable and the cake was incinerated.
- What set the project apart?
-
Processing phosphorus demands many safety measures. The presence of materials containing phosphorus mean that there are still support services stationed on the Thermphos grounds. Petrogas integrated the installation within the former plant to assure the safest possible processing.
- What were the project challenges?
-
“The complexity of the project was a challenge, particularly since there are just a handful of phosphorus plants worldwide. Our processing installation had never been built before. Wherever possible, Petrogas made use of the knowledge and experience of former Thermphos employees. “
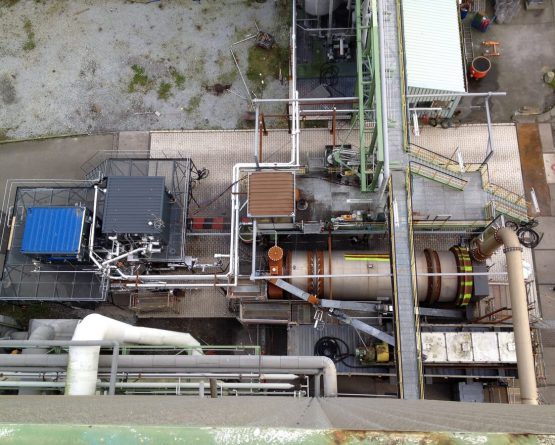
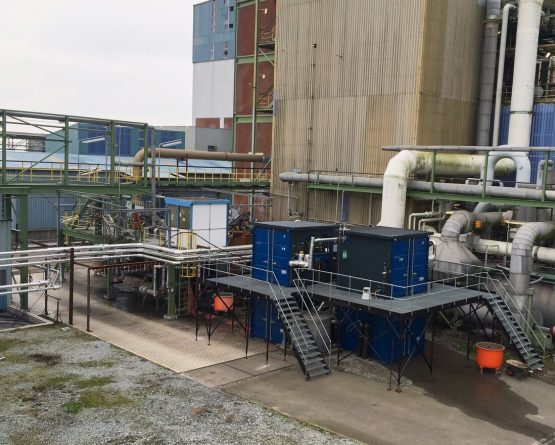
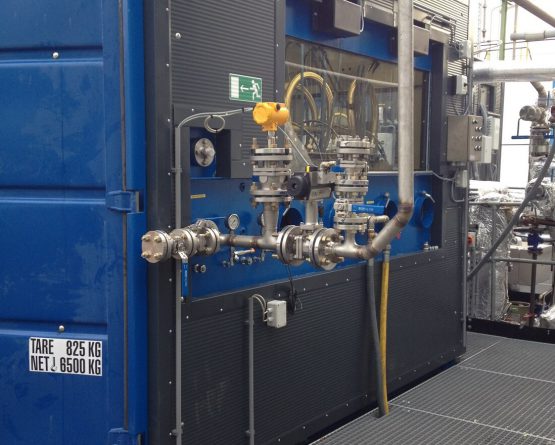
- What did our customer request?
-
ProLabNL – based in Arnhem, the Netherlands – offers testing facilities that simulate oil field conditions with natural gas/raw oil and water (hydrocarbons) under high pressure, for instance to test liquid separators. Petrogas was approached by ProLabNL to create a high pressure test facility for subsea liquid separation.
- Our solution
-
The installation was designed based on information provided by ExxonMobil for the testing of a subsea separator. ProlabNL used this information to create a process flow diagram, which Petrogas then elaborated into a piping and instrumentation diagram with the required materials list. Next, Petrogas provided for the 3D installation drawing, wiring diagrams and the purchase of components such as pumps, instrumentation, flow meters and valves.
- What set the project apart?
-
Withing Petrogas we established a close partnership with our customer in order to ensure the best performance of this test facility. Specially with respect to the material we used and the short notice changes we have performed successfully. The material which was used is suitable for the highly corrosive atmospheres and fluids. The opening of this project was performed by a member of the Royal Dutch family.
- What were the project challenges?
-
“The installation had to be designed in such a way that it would fit in the available space, that any emitted vapours could not be ignited by the nearby rail track, and that the could be depressurised within a certain amount of time. Petrogas furthermore supplied the information required for the nuisance act license and the fire department.”
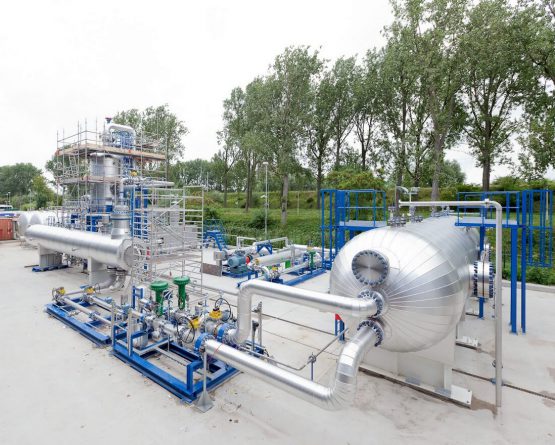
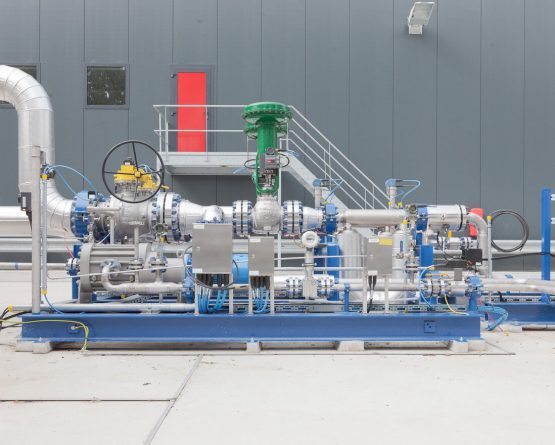
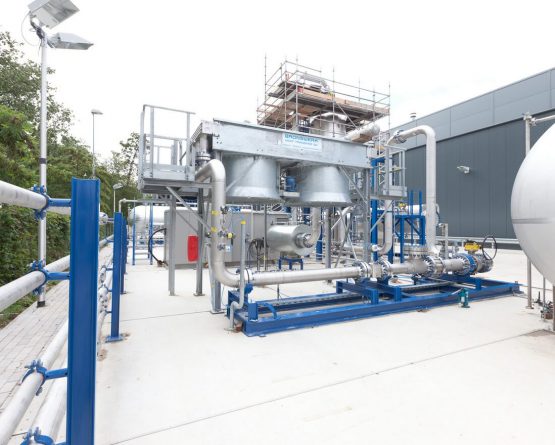
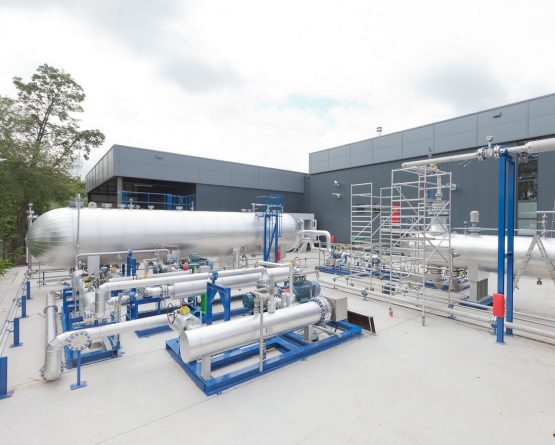
Contact us
Would you like to discuss your project with our Experts? Please feel free to contact us.
Direct contact with our Experts
Your interest
Custom engineering
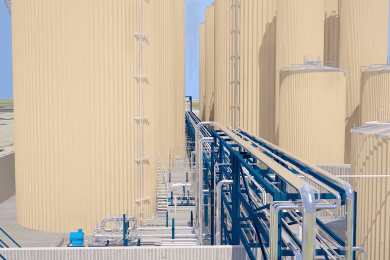